What to Remember when Selecting a Cutter
Think carefully about the length of cutter you need as biggest is not always best. The aim is to try and maintain accuracy and minimise vibration, but at the same time maximise safety. So it is not always advantageous to buy a cutter with long cutting edges if you don’t need them. In fact, if you start cutting really deep in one pass the cutter will deflect and vibrate excessively.
For deep cuts, plunge in gradually with several shallower passes. The longer the cutter is, the more this vibration is likely to occur and in extreme cases you can actually snap the cutter, usually at the point between the flutes and the shank.
Shorter bits are obviously more stable and will cut smoothly. Another strength consideration involves the shank diameter. Always choose the largest diameter shank that your router will take.
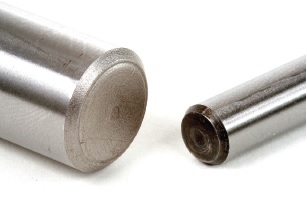
There is rarely any significant difference in cost, but the extra stability involved is proportionally huge. A 1/2” shank has a cross sectional area that is four times that of a 1/4” shank which says it all in terms of strength.
Don’t think that buying a small diameter shanked cutter and then bushing it up to fit a bigger collet is a way round this. These bushes can never grip the cutter as accurately as a collet and they inevitably introduce yet another source of vibration, so avoid them if at all possible.
When choosing a cutter, a good rule of thumb is that the cutting edge length should not exceed three times the diameter and if you can get away with less, then so much the better.
The choice of cutter grade is also critical. For most jobs, TCT is the only option for its excellent edge holding properties in a broad range of different wood based materials. But not all tungsten carbide is of the same quality, and just being labelled TCT doesn’t necessarily signify a good cutter.
The grade of carbide has improved markedly on the top quality bits and in recent years a micro-grain carbide has been introduced which can be sharpened to a fine edge without becoming brittle or chipping, a recurring problem with early cutters. There can be as much as a ten times difference in the edge holding properties between different grades of carbide, so always insist on micro-grain.
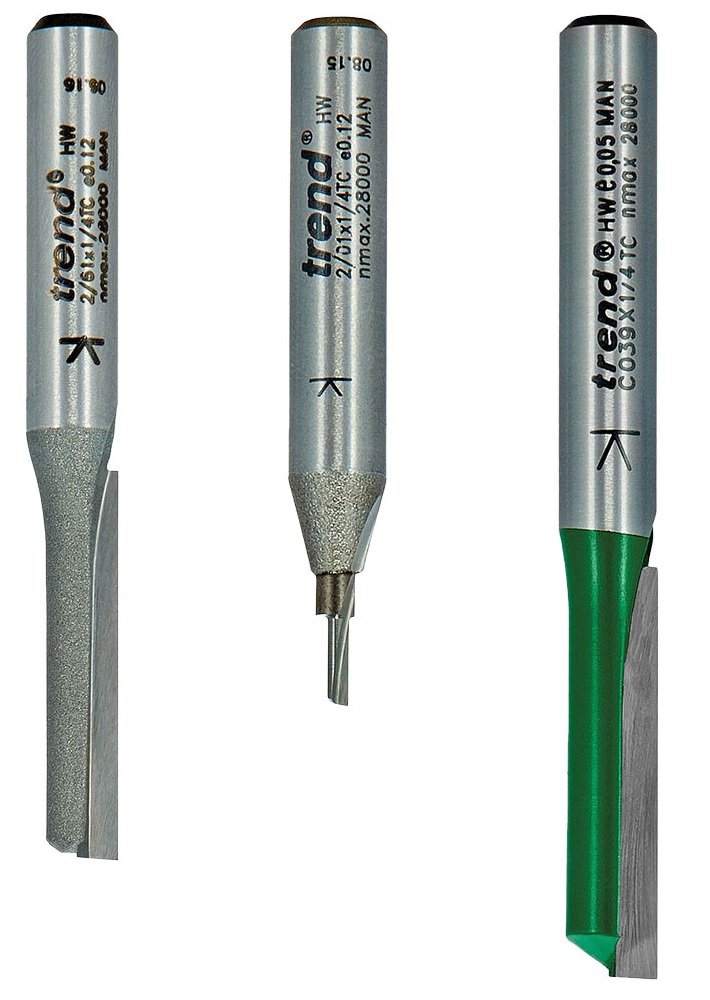
Only choose HSS if you want a superfine finish in softwood and are able to keep the edges in shape with regular honing. The case for deciding between a single or two flute cutter is even more clear-cut. If a fast feed speed is your most important consideration then go for a single flute version, but it is nearly always better to go for a two flute cutter, which will leave a noticeably superior finish to its single flute counterpart.
If the cutter of your choice is available in shear or spiral form then this is another way of making the cut smoother and cleaner, particularly in tricky, end-grain trimming work. They also reduce the load on your router and are more comfortable to use for long periods. However, this option is more expensive than a straight two flute cutter and you will only be able to hone the shear type.
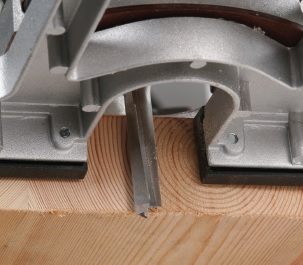
Examine the Quality of your Router Cutter
How do you go about checking the quality? Although you cannot tell much about the raw material of the cutter just by looking at it, there are other visible signs on the cutter like machining quality, grinding angles and surface finish that will give a good indication as to quality. A manufacturer is unlikely to buy the best quality material and then spoil it by poor machining. A careful examination is likely to reveal whether the cutters are up to standard or not and it is a worthwhile operation, as the quality is reflected in both your subsequent work and safety.
Some new cutters come covered with wax, which although protective can also hide manufacturing imperfections. Remove this carefully after slitting it with a knife, but beware as it is very easy to cut yourself as you slide the wax free, so consider wearing gloves for this operation. Then have a really close look at the cutter. See if the cutting edges are really sharp and make sure that the brazed tips do not overhang the end of the flute other than by the ground bevel, as this can cause them to flex under load.
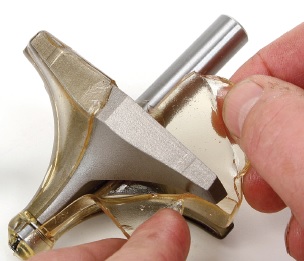
Check that the surface of the edges are not chipped or pitted and the edges themselves are honed smooth and polished. The best way to do this is to rub your fingernail down the ground angle. If it feels rough or wavy the edge is not properly machined. It needs to be a mirror finish otherwise the cut surface will be equally rough and resin will soon start to build up in the grooves and affect the quality of cut.
Each cutting edge must be ground to the same angle to ensure that they are doing an equal amount of work, so they must be precisely the same size and shape. Cheap cutters have very thin carbide tips that leave little scope for re-sharpening. As well as giving longer life, a thicker tip will give much more support to the edge and will stay sharp longer.
Check that the brazing on these tips is clean and that there are no gaps or voids, or the tip may detach itself under load. Poor quality brazing will also affect the ease of chip clearance. The shank should be smooth and perfectly true, with a nicely chamfered end and most importantly, dead on size.
If you have any doubts, check the diameter with a micrometer, as an undersized one will very quickly damage the collet. Then if possible, put the cutter into the router and feel how it spins, it must run free of any vibration.
If you are buying a bearing guided cutter, check that the mounting pin is strong enough to support the bearing and that the holding screw tightens sufficiently to get a good hold, but the bearing itself should have minimal play whilst still turning freely.
Finally, look for a cutter supplied in some rigid packaging that allows for quality protection and storage, and where necessary, instructions for use should be included, particularly with the more complicated profiles.
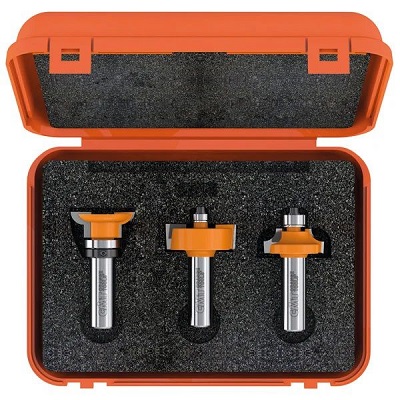
Use our Guides to Router Cutters to help you even further in your decision.